CO-ROTATING BI-HOLE BARREL: MAGNETOSCOPIC INSPECTION FOR EXTRUSION IN THE OIL INDUSTRY.
Challenge: In the oil industry, the reliability and quality of the components for the production of plastic materials are essential. Euroviti has recently completed a service work on a nitrided co-rotating bi-hole barrel with welded cooling system, designed to ensure high-performances in the extrusion processes.
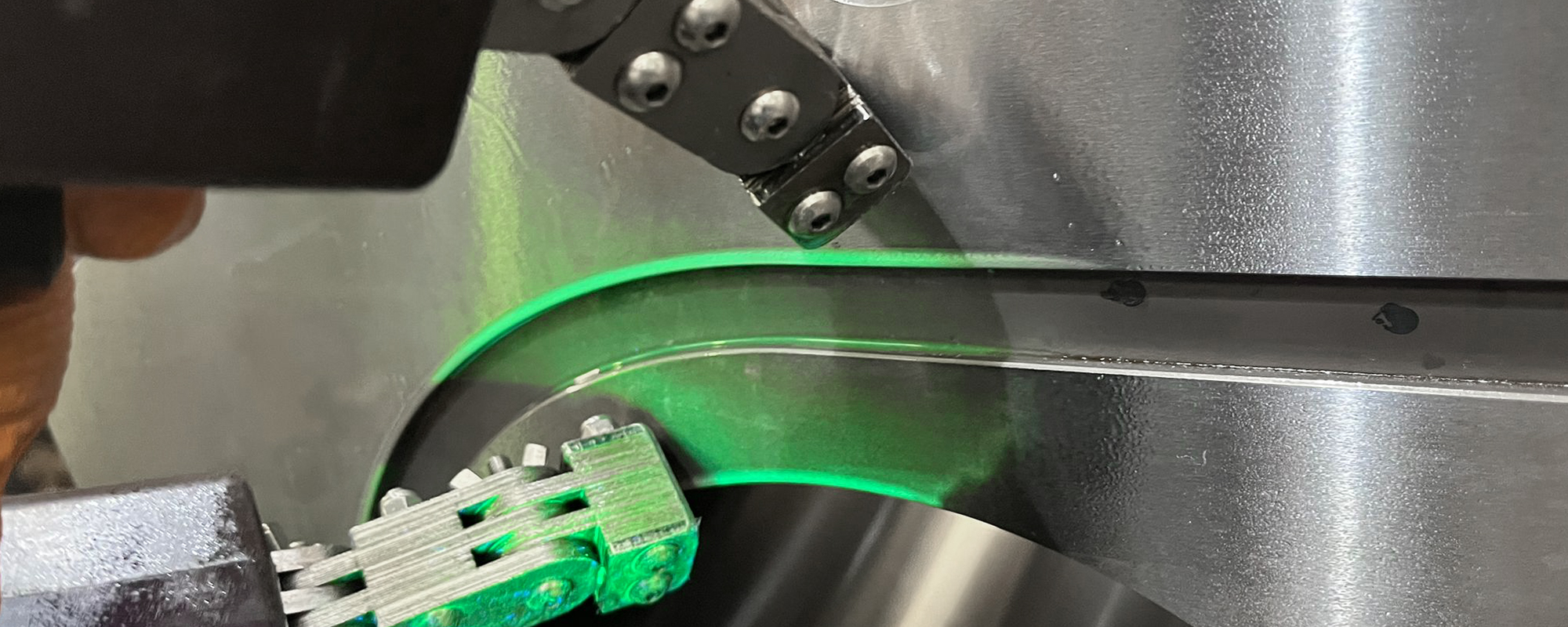
Components’ features: The co-rotating bi-hole barrel, made in high-quality nitrided steel, is equipped with an advanced integrated cooling system. This type of barrel is mainly used in extrusion processes in the oil industry for the production of plastic materials, where maintaining thermal stability and consistent production is fundamental.
Inspection procedure: To verify the quality of the component, we performed magnetoscopic inspection with fluorescent liquids. This non-destructive method was particularly efficient to identify superficial cracks and discontinuities, especially in the welded and subjected to cyclic stresses areas. The use of this method allows to identify the most subtle defects, guaranteeing a high level of reliability.
Magnetoscopic inspection’s advantages: Magnetoscopic inspection with fluorescent liquids ensures numerous benefits for high-precision components such as co-rotating bi-hole barrel:
- Accurate detection of fatigue cracks and superficial discontinuities;
- Failure prevention through advanced diagnostic;
- Adaptability for complex components, such as barrels with welded cooling systems.
Results and conclusions: Magnetoscopic inspection represents a key solution to ensure the quality and durability of components intended for the oil industry. Euroviti’s work on this co-rotating bi-hole barrel shows our commitment in providing customized and advanced technologies, capable of meeting the needs of the most demanding customers.