ZERO SCRAP, MAXIMUM PERFORMANCE:CUSTOM SCREW DESIGN FOR R-PET PROCESSING.
When it comes to attention to the environment, plastics is always in the eye of the storm, as if the problem was the material itself and not the final use made out of it. That is to say, what happens when a product finishes its life cycle in the hands of the consumer. Among the most debated and striking cases there are PET containers. Are we sure that after that the life cycle of a product is realty over?
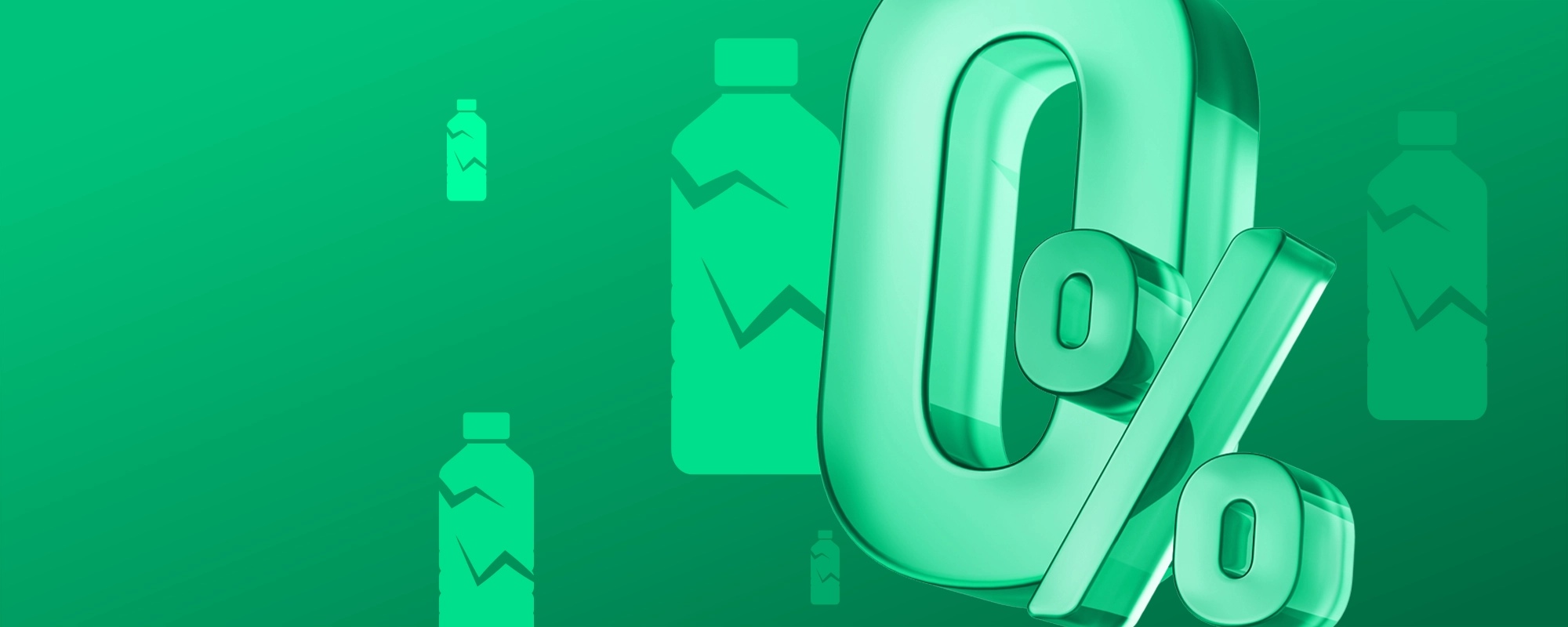
Surely, the best-known use of R-PET currently is the containers’ one. In one of the latest projects we have, in fact, helped one of our customers, a leader in supply of infant products, to solve and stabilize a production process of jars made in 100% recycled PETwith a density of 1.5 g/cm3 and a glass transition at 79 °C.
In this specific case, we did not need to modify neither the injection blow moulding machine nor the plasticizing unit; after the analysis of our technical department, they noticed the L/D ratio of the original plasticizing unit was considerably too low and that the feed section of the screw, being „for general purpose“, didn’t meet the necessary process needs. Therefore, it was causing problems of feeding first, and slipping then, resulting in a high percentage of scrap of the finished pieces.
Thus , the solution was not only a re-designed screw profile, but a restructure of it. By that, we made it able to compensate the L/D ratio, thanks to the development of the helix along with a dedicated final mixer based on the specific characteristics of R-PET material.