FROM CORN TO CAR:A CUSTOM INJECTION SCREW FOR PLA.
A valued customer approached us with a unique request: the development of a customized screw specifically designed for injection moulding with PLA polymer for an Automotive application. Understanding the specialized demands of working with biodegradable materials like PLA, our team quickly mobilized to deliver a tailored solution that enhances processing efficiency and ensures optimal performance. But why a tailored solution was needed?
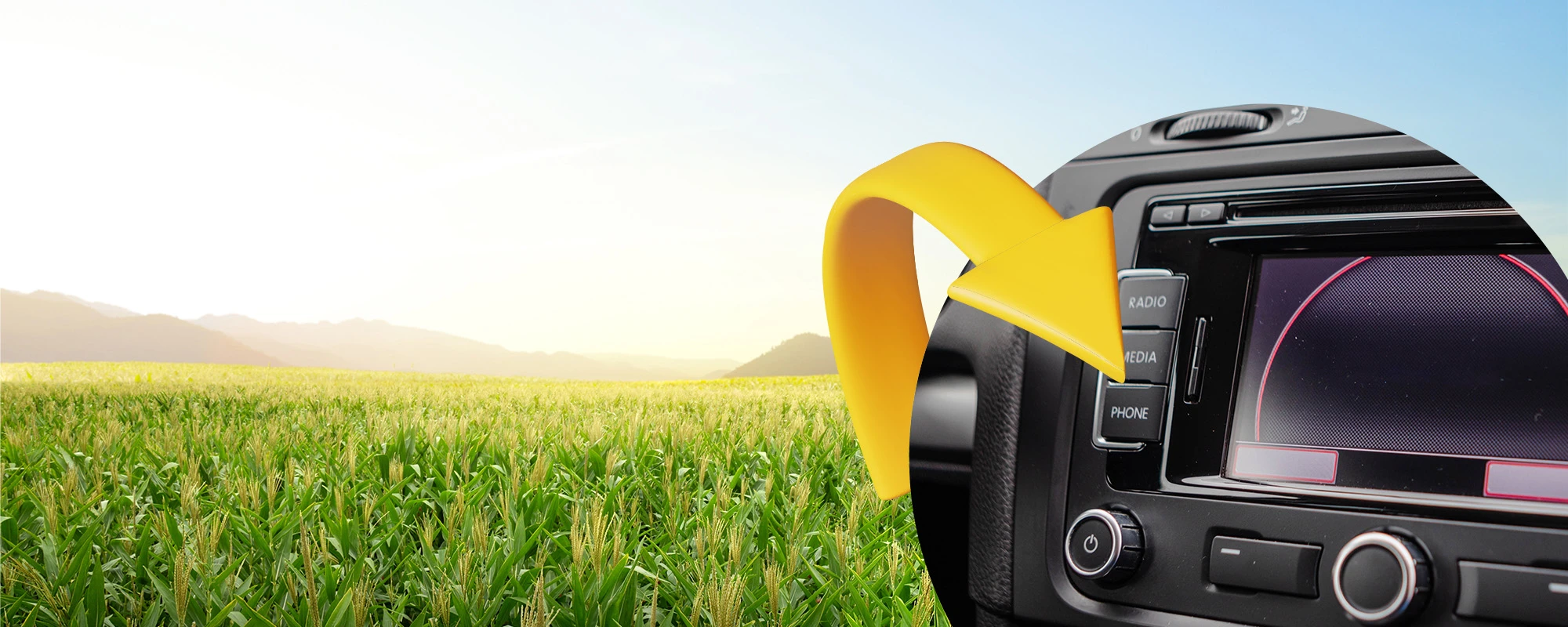
Polylactic acid (PLA) — a biopolymer derived mainly from renewable sources like corn starch and sugarcane — was once a niche curiosity. Today, it’s firmly entrenched as one of the top three biodegradable plastics globally. Modern PLA grades exhibit an impressive range of properties: transparency, high gloss, and mechanical strengths comparable to conventional petroleum-based materials like PET. Despite its attractive properties, PLA demands a refined approach to injection moulding.
Treating PLA like a standard thermoplastic is a recipe for costly failures. Here’s why: PLA is hygroscopic, meaning it readily absorbs atmospheric moisture. If improperly dried, this moisture can cause hydrolysis during melting, breaking down polymer chains and degrading mechanical properties. The plasticizing unit — particularly the screw design — plays a critical role in preserving the integrity of PLA during processing. For instance, excessive shear not only causes thermal degradation but can severely impact molecular weight, altering the final product’s strength and clarity. Additionally, cycle times, residence times, and volumetric ratios must be optimized. Shorter residence times at stable melt temperatures help avoid degradation, while careful mould temperature management ensures good surface finish and dimensional stability.
PLA and other bio-materials may not yet replace every conventional plastic, but with the right tools — including custom screws and tailored moulding conditions — they are already reshaping how we think about manufacturing, sustainability, and innovation. The real question now is: Are manufacturers ready to adapt as quickly as the materials themselves are changing? At Euroviti, the answer is a resounding yes.
With decades of expertise in designing and manufacturing high-performance screws, barrels, and plasticizing units, Euroviti is fully prepared to support customers in adapting to the unique demands of bio-material processing. Whether for injection moulding or extrusion applications, our team offers solutions that optimize material handling, improve product quality, and extend spare parts life — even when working with sensitive and fast-evolving bioplastics like PLA.