PERFECT SHOT-TO-SHOT REPEATABILITY WHILE MIXING
In the past we introduced to our followers what could be considered an old technical solution: the Mixing Screw-Tip assembly. A product that which we improved during the years in relation with new polymers, additives and we explained where and when it can be considered a good solution. Today, following costumers’ positive feedback we introduce one of our latest successes, another innovation and development made on such product category.
The last challenge was posed to us by one of the world most famous brands of injection moulding machines which requested the help of our technical department to solve a problem of maintaining the cushion values and shot repeatability with very low injection shot’s volumes. The issue had to be solved on moulded parts, produced on different size of machines and plasticizing unit, to produce automotive products and for medical component, both scenarios involved highly technical parts as regards the structure of the piece, the mould flow, and with an extreme need for aesthetic perfection in both costumers’ necessities.
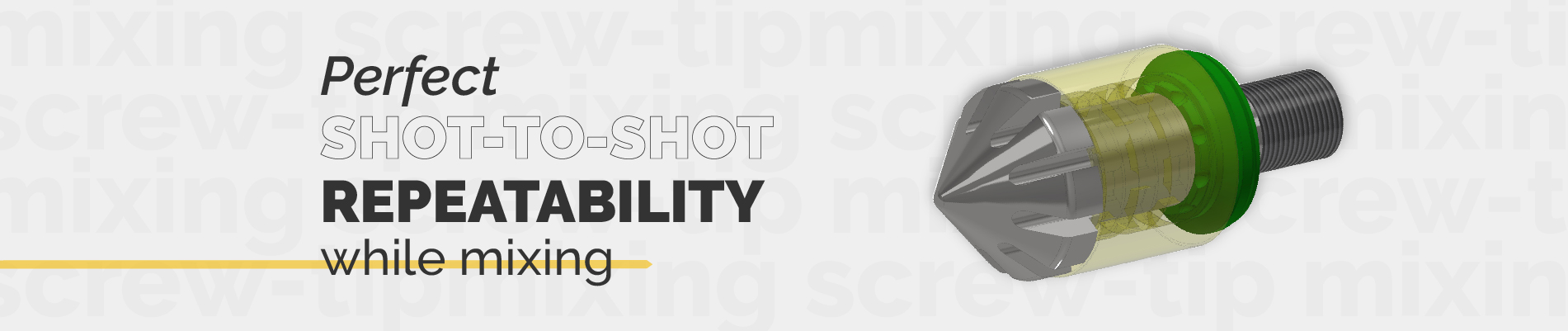
If you are wondering why this issue is related to mixing screw-tips, the answer is that this was not the only problem with the customers having both mixing and homogenizing problems because of a small shots’ volumes and low residence time. In one case it was used for PC/ABS + colourant compound and in the other it had to process ABS + colourant or PE + colourant as they say in these cases, we have been called to take two birds with one stone.
The OEM which cooperated with us in the past, contacted us after changing several screw-tips, their check-ring tolerances and after assessing that none of the barrel was worn and that the purging compound was not helping since the cause wasn’t any degraded material build up in this area and there was nothing causing the valve to not seat properly.
Because of the small shot, costumers were used to work on the machine parameters, back-pressures, RPMs, packing after injecting and so on… but the shots were never perfect, and the unsatisfactory aesthetic characteristics were the only constant thing. We therefore created a new geometry of the tip and the check-ring, modifying their design for a fast-closure while ensuring the correct amount of material that could pass without exerting too much friction in the passage between check-ring and seat-ring: resulting in a quick-closure mixing screw-tip.
The result, with standard process parameters, was more than satisfactory; but not satisfied with a standard result, the end user tried to use even more extreme process parameters to optimize the cycle time… the result therefore became excellent, since there was not the slightest deviation of the cushion value, and the investment was re-paid in 4 hours of machine running. Feel free to contact us for any further question, curiosity, or inquiries.
Today, following costumers’ positive feedback we introduce one of our latest successes, another innovation and development made on such product category.